Deep Pour Resin For DIY Epoxy River Tables
Pouring epoxy resin river tables require certain types of epoxy and certain techniques. Most coating epoxies require thin pours of no more than 1/8 to 1/4" per application. Because many DIY epoxy river tables are much thicker than 1/8 inch, either multiple layers must be used or a thinner, slower curing epoxy must be used.
Casting Resin for River Tables
How To Make An Epoxy River Table
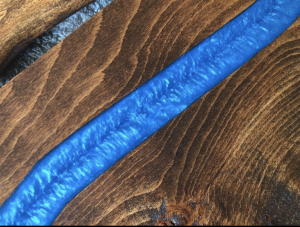
@love_of_the_grain_workshop
Whether it is a live edge river table or a simple coffee table with a river, prep is almost always necessary. In addition to prepping the surface, as done with any epoxy table, a river project normally requires a frame or dam on either end of the river. Because most epoxies self level, a dam is necessary to prevent the epoxy from flowing out. Essentially, the dam or frame will allow the epoxy to be built up thicker than the self leveling thickness. Most coating epoxies will self-level to 1/16" to 1/4". This is why choosing the best epoxy for your river table project is paramount.
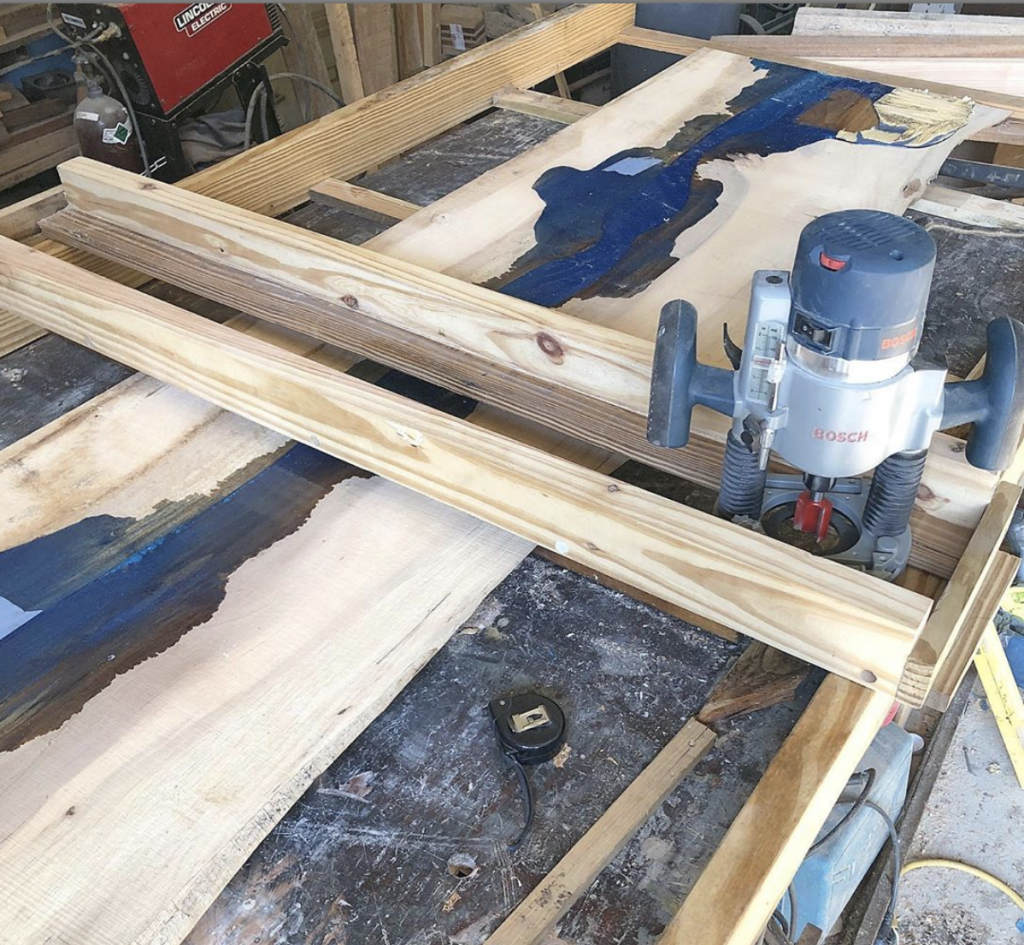
@love_of_the_grain_workshop
When making a dam, it is important to consider whether or not the epoxy will adhere to the material used. Many people are inclined to use a wooden frame (not treated) and are disappointed to discover the epoxy sticks to the frame. This will result in pounding, wedging, prying and sanding to remove the frame. Needless to say, it's important to choose the frame materials wisely.
Pro Tip: Most epoxies will not stick to silicone and certain tapes. A cheap option is to use clear packing tape as the epoxy will not stick to it.
Deep Pour Resin
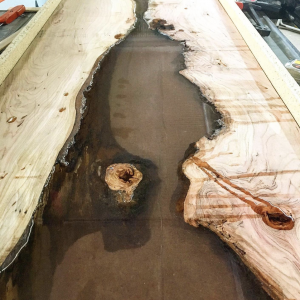
@goodviewwoodworks
After the project has been properly prepped, taped, and dammed off, it's time to mix and pour the epoxy. Pouring epoxy too thick can ruin an entire project. As previously mentioned, most coating epoxies like Table Top & Bar Top Epoxy require thin pours of no more than 1/4 inch per application. For a table that is to be 2" thick, this would require 9 pours of epoxy, including the seal coat. Mixing and pouring epoxy this many times is not only time consuming, but makes the project susceptible to dust & particle exposure.
An alternative to using a coating epoxy is thick pour epoxy resin or casting resin. These types of resins are thinner in viscosity and generate lower exotherm, thus can be poured much thicker. The caveat is that these types of resins take much longer to cure, often 36-48 hours. The downside to long cure times, is more time for foreign substances (i.e. bugs, dust, hair, etc) to land on the project. Additionally, thinner epoxy requires a tighter dam/frame--thin epoxies tend to work behind loose dams and ultimately seep through.
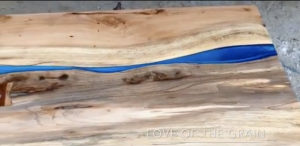
@love_of_the_grain_workshop
Each type of epoxy has Pros and Cons when pouring a river table project. Somes crafters find working with a coating epoxy easier, while others find a single pour easier. One advantage of pouring multiple layers (whether using a coating or thick pour epoxy) is that it allows for corrections to be made along the way. For example, if bubbles were to develop early in the project, they could be sanded down and then recoated.
Cured Epoxy Must Be Supported
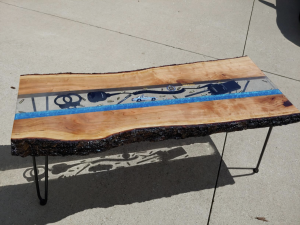
Once cured, epoxy river tables MUST be supported. Cured epoxy is not flexible--if the table/project is allowed to flex, the cured epoxy can crack. This is especially true when epoxy is used to fuse two slabs/live edges of wood together, or when the river is exposed on top and bottom of the project. Supporting the project can come in all shapes and sizes and the woodworkers out there cease to get creative with support systems--suffice it to say that cured epoxy must be supported.
Thick pour applications must consider how porous the substrate is.
Some people may be inclined to prep the project and immediately pour multiple inches thick, without considering sealing the project first. Most river tables are constructed out of wood, which is very porous. Without sealing the wood prior to a thick pour, bubbles could remain in the epoxy as it cures. The best way to prevent bubbles is to seal the project with a very thin seal coat of epoxy. A thin seal coat allows the epoxy to flow into all porous areas of the project and the air to easily rise to the surface, and ultimately be eliminated.